Promotion
Das IAAM erweitert durch zahlreiche Promotionen den wissenschaftlichen Wissensstand.
Laufende Promotionsvorhaben
Development of a semantic interoperable model for generic I4.0 field devices
Die Erhöhung der Flexibilität in der Automationsbranche und die Einbeziehung von Technologiestrategien aus dem bekannten Industrie 4.0 Konzept erfordert die Entwicklung neuer Methoden für deren vollständige Integration. Ein zentraler Aspekt von Industrie 4.0 ist das Zusammenwirken der „Dinge“. Dies erfordert, dass „Assets“, wie sie in DIN SPEC 91345 beschrieben sind, Informationen gemeinsam nutzen, was ohne Semantik nicht möglich ist.
Heutzutage werden in der Industrie herstellerabhängig unterschiedliche Kommunikationsstandards und Datenstrukturen verwendet, wodurch eine Integration nach der gleichen Methodik nicht gewährleistet werden kann. Darüber hinaus erfordert die Entwicklung intelligenter Geräte die Integration verschiedener Funktionalitäten, sogenannter Profile, die ihr Verhalten beschreiben können. Daher können die Entwicklung, die Gerätetests und die Integration in der Automatisierungsindustrie für diese neuen intelligenten Geräte vergleichsweise umständlich sein und ein gesondertes Vorgehen für jeden einzelnen Anwendungsfall erfordern. Außerdem wird die Wiederverwendbarkeit derselben Technologie und Konzepte für andere Anwendungen beeinträchtigt.
Aus diesem Grund ist es das Ziel dieser Arbeit, ein semantisches Modell zu erstellen, das generische Funktionalitäten und Kategorien für die Realisierung dieser intelligenten Geräte ganzheitlich integriert.
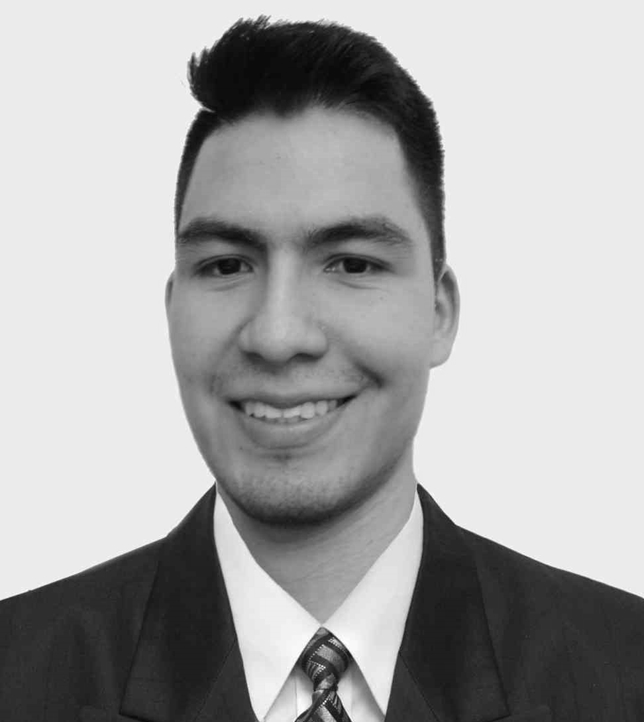
Research on producing complex metal parts by Laser Powder Bed Fusion, to be welded onto larger components
Das additive Fertigungsverfahren Laser Powder Bed Fusion bietet ein herausragendes Potenzial zur Herstellung konturnaher funktionsintegrierter Bauteile aus metallischen Werkstoffen. Durch den schichtweisen Aufbau begegnet das Verfahren den Forderungen nach steigender Komplexität und steigender Flexibilisierung herzustellender Produkte. Trotz der Vorteile dieser jungen Fertigungstechnologie wird sie aktuell vornehmlich zur Herstellung von hochwertigen bzw. kostenintensiven Bauteilen in kleinen Losgrößen eingesetzt. Industrielle Anwendungsbeispiele finden sich primär in den Branchen Luft- und Raumfahrt, Energietechnik und Medizintechnik. Ursache für den derzeitigen limitierten industriellen Einsatzgrad der LPBF-Technologie sind die fehlende Einbindung des Verfahrens in die vorhandenen industriellen Prozessketten, die geringe Produktivität und die eingeschränkte herstellbare Bauteilgröße.
Der in dieser Promotion verfolgte, vielversprechende Ansatz diesen Herausforderungen zu begegnen, beinhaltet die intelligente Kombination des LPBF-Verfahrens mit dem Fügeprozess Schweißen. Ziel der Arbeit ist die Entwicklung einer ganzheitlichen Prozesskette zu Herstellung von großvolumigen und funktionsintegrierten Bauteilen mittels additiver Fertigung und Schweißen.
So könnten Bauteilbereiche, die komplexe und funktionsintegrierte Elemente enthalten, mittels LPBF gefertigt werden, während andere Bereiche, die konventionell (Zerspanung, Umformen) kosteneffizienter gefertigt werden können, mit bestehenden Fertigungsverfahren hergestellt werden. Außerdem ist es denkbar, den möglichen Bauraum von LPBF-Konstruktionen durch das Verschweißen von mehreren LPBF-Teilen zu vergrößern.
Dem gegenüber stehen viele metallurgische sowie prozesstechnische Hindernisse, die im gegenwärtigen Stand von Wissenschaft und Technik noch nicht ausführlich diskutiert wurden. Die ersten Schritte des Vorhabens beinhalten, nach einer tiefgehenden Recherche, die Anpassung des LBPF-Prozesses zur Reduktion resultierender Eigenspannungen. Materialsimulationen werden ebenso Einsatz finden, wie eine detaillierte Betrachtung der auftretenden Temperaturgradienten entlang beider Fertigungsprozesse. Gestützt durch regelmäßige metallurgische Untersuchungen wird versucht Verzug zu minimieren und metallurgisch vollständige Verbindungen zu erzielen.
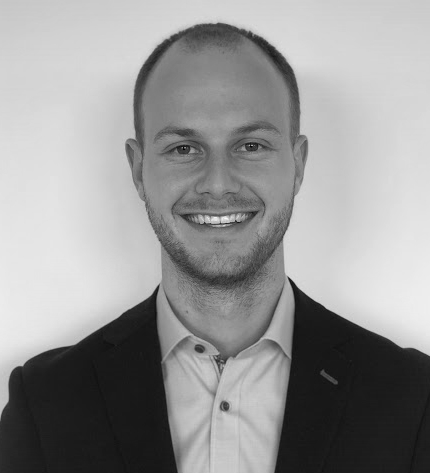
Analyse und Gestaltung manueller Arbeitstätigkeiten unter ergonomischen Gesichtspunkten zur Reduzierung und Stabilisierung von Taktvarianz zur Optimierung der Prozessplanung
Die Reduzierung von Taktvarianz in der Prozessplanung stellt eine wesentliche Herausforderung für moderne Produktionssysteme dar. Insbesondere in der Wertstromanalyse und der Methoden-Zeit-Messung (MTM) fehlen derzeit Ansätze, die menschliche Variabilität adäquat berücksichtigen. Faktoren wie Ergonomie, Motivation und Wissensstand sind entscheidend für die Stabilität und Qualität manueller Arbeitsprozesse, werden jedoch in traditionellen Ansätzen häufig als statisch angesehen. Kurz- und langfristig lassen sich jedoch dynamische Charakteristiken identifizieren, welche in der Prozessplanung als statisch angesehen werden.
Menschzentrierte Arbeitsprozesse unterliegen erheblichen Schwankungen in Effizienz und Qualität, die durch ergonomische Belastungen, unzureichende Wissensvermittlung und motivationale Defizite bedingt sind. Klassische Verfahren der Wertstromanalyse und MTM erfassen Prozessabläufe zwar strukturiert, erlauben jedoch keine ausreichende Individualisierung und sind nicht reaktiv in Bezug auf dynamisches Verhalten. Diese Limitationen erschweren die Prozessplanung von Montagelinien, Identifikation von Optimierungspotenzialen und die nachhaltige Reduktion von Prozessvariabilität.
Im Rahmen dieses Promotionsvorhabens wird ein ganzheitliches System entwickelt, das Gamification-Ansätze, ergonomische Optimierung und dynamisches Wissensmanagement integriert. Aktuell werden Systeme entwickelt, die detaillierte Ergonomie-Analysen zur Quantifizierung individueller Belastungen ermöglichen und gamifizierte Mechanismen zur Steigerung der Motivation integrieren. Ein datenbasiertes Wissensmanagement wird implementiert, das Informationen in Echtzeit bereitstellt und dynamisch an den situativen Bedarf anpasst. Unter Einsatz von maschinellem Lernen, insbesondere Reinforcement Learning, werden adaptive und dynamische Systeme entwickelt, die Daten aus einer erweiterten Wertstromanalyse nutzen. Dabei erfolgt eine differenzierte Betrachtung der einzelnen Arbeitsschritte, einschließlich Durchführungs-, Interpretations- und Korrekturzeiten. Diese granularen Daten fließen in die Modellierung und Simulation ein, um präzise Strategien zur Stabilisierung von Prozessen und Reduktion von Variabilität zu entwickeln. Ziel ist es, durch diese detaillierte Analyse personalisierte und effiziente Arbeitsabläufe zu schaffen.
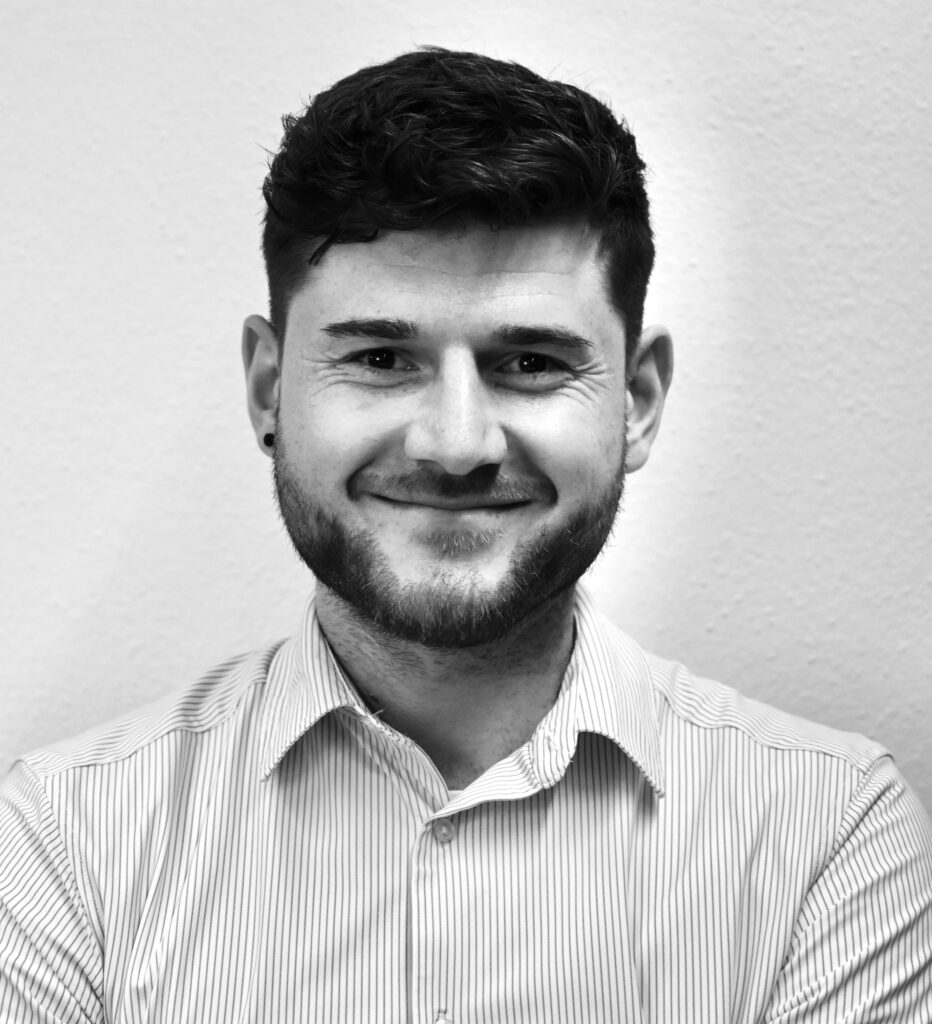
Entwicklung eines skalierbaren Klebprozesses für das strukturelle Fügen von Bambusrohren in digitalisierten Fertigungsketten
Bambus ist ein schnell nachwachsender Rohstoff mit hohen Festigkeiten und geringem Gewicht, der fossile Werkstoffe, wie Metalle und Kunststoffe, in zahlreichen Produkten ersetzen kann. Ziel des Projekts ist die Entwicklung einer schnellen, einfach automatisierbaren, mechanisch hochbelastbaren und ökologisch nachhaltigen Fügemethode, um ganze Bambusrohre („full culm“) stoffschlüssig zu verbinden. Herkömmliche Fügemethoden, wie Schraub- oder Wickelverbindungen, sind meist aufwendig in der Herstellung und weisen nur geringe Tragfähigkeiten auf, welche die mechanischen Eigenschaften von Bambus nicht vollständig ausnutzen.
Im Promotionsprojekt wird eine neuartige Steck- und Klebverbindung („Klebmuffe“) untersucht, die an der FH Aachen entwickelt und zum Patent angemeldet wurde. Konkret werden mechanische Versuche mit verschiedenen Klebstoffen und verschieden oberflächenbehandeltem Bambus durchgeführt, um möglichst hohe Klebfestigkeiten zu erzielen. Darauf aufbauend wird die Klebmuffe klebgerecht gestaltet und für einen beschleunigten, kosteneffektiv skalierbaren, automatisierbaren Fügeprozess optimiert. Ergänzend wird untersucht, wie sich die Ökobilanz eines Produkts durch den Einsatz von Bambusrohren anstelle von anderen Materialien verbessern lässt. Die Forschungsergebnisse sollen neue industrielle Anwendungen für Bambusrohre ermöglichen, um den Bedarf fossiler Werkstoffe zu reduzieren.
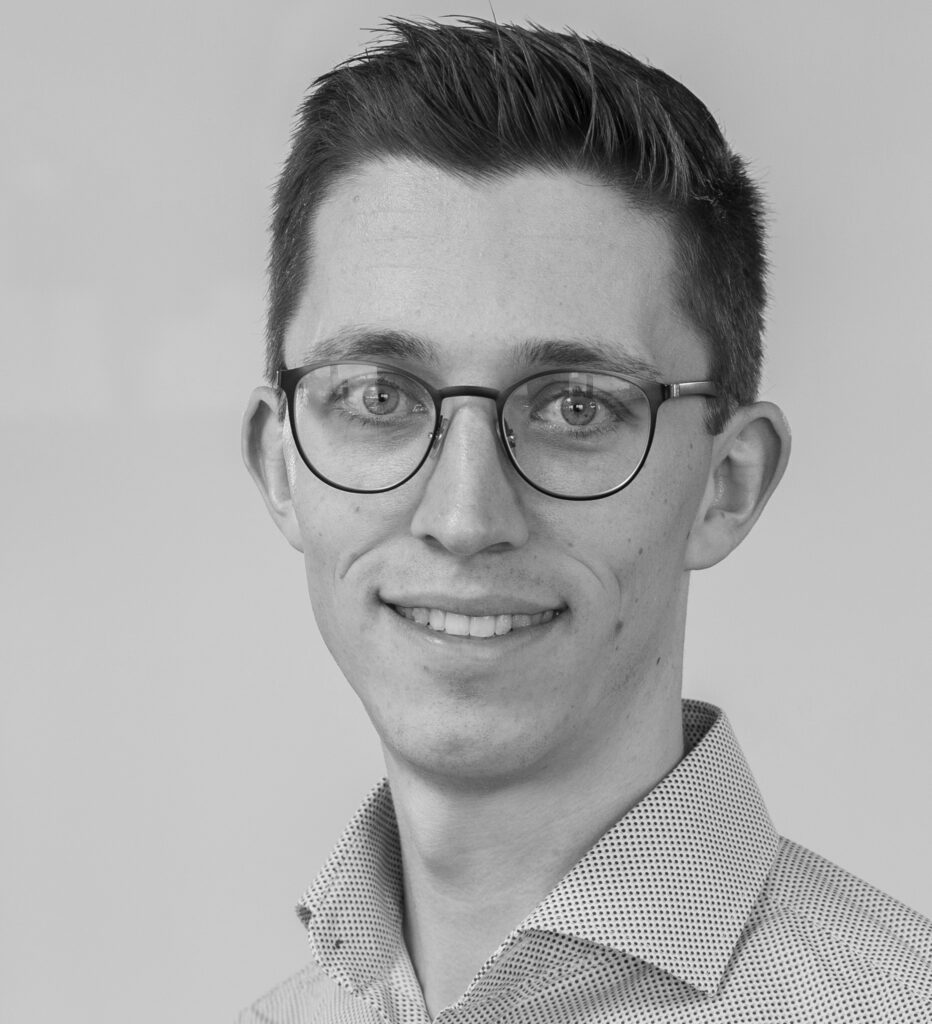
Management von verwalteter Software für zuverlässige, eingebettete Sicherheitssystemen am Beispiel von Brandmeldeanlagen
Brandmeldeanlagen (BMA) spielen eine zentrale Rolle im vorbeugenden Brandschutz, indem sie Brände frühzeitig erkennen und Alarm auslösen, um Personen zu warnen und Schäden zu minimieren. Ein wesentlicher Bestandteil moderner BMA ist die Software, die aktuell im wesentlichen durch Wartungspersonal aktualisiert wird.
Um eine Aktualisierung der Software aus der Ferne zu ermöglichen, bedarf es eines sicheren und robusten Softwaremanagements. Im Rahmen des Projekts werden anhand von Use Cases spezifische Anforderungen an die Software, die Hardware und das Gesamtsystem erarbeitet, um einen sicheren und zuverlässigen Update-Mechanismus zu gewährleisten. In enger Zusammenarbeit mit relevanten Fachverbänden werden Richtlinien entwickelt und entsprechend erprobt, die dazu beitragen, die Zuverlässigkeit und Sicherheit des Softwaremanagements nachweislich zu gewährleisten.
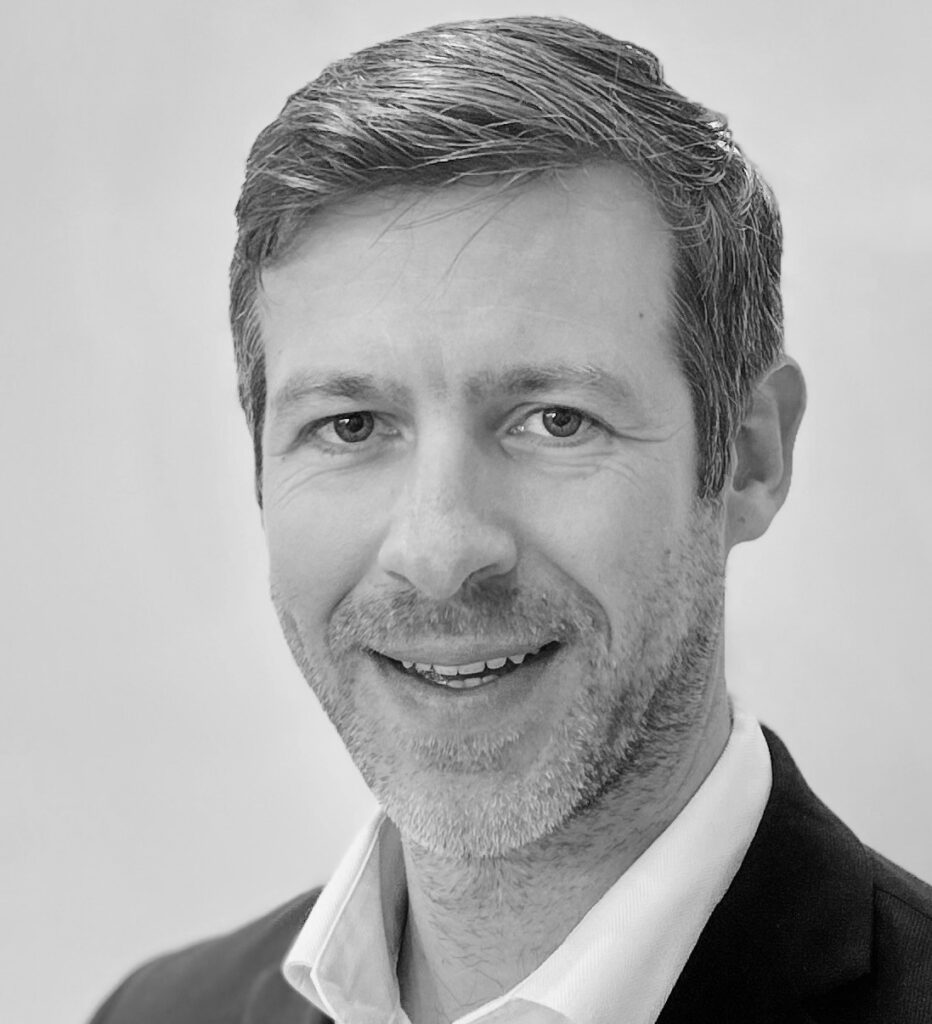
Visuelle Roboterinspektion Strukturierter Freiform-Oberflächen mittels Anomalieerkennung
Jahrzehntelang hat sich die Fertigung hauptsächlich auf die Produktion von kleinen Stückzahlen mit hohem Volumen gestützt. Die Trends in der Branche gehen jedoch in Richtung High-Mix- und Low-Volume-Produktion, was neue Herausforderungen für die Automatisierung mit sich bringt. Herkömmliche Automatisierungslösungen für niedrige Stückzahlen und hohe Stückzahlen sind oft kostspielig, unflexibel und ungeeignet für verschiedene Produkttypen, was sie für kleine und mittlere Unternehmen (KMU) unpraktisch macht. Darüber hinaus benötigen diese Systeme viel Platz und Hochgeschwindigkeits-Automatisierungsmodule, die in KMU-Umgebungen oft unnötig sind. Infolgedessen verlassen sich viele KMU weiterhin auf die manuelle Qualitätskontrolle, obwohl sie mit einem Mangel an qualifizierten Arbeitskräften und zunehmendem finanziellen Druck zu kämpfen haben.
Diese Forschungsarbeit konzentriert sich auf die Entwicklung von automatisierten Qualitätskontrolllösungen für strukturierte Freiformflächen in der Fertigung mit hohen Stückzahlen und geringen Stückzahlen. Das Kernstück dieses Ansatzes ist die 2D-Anomalieerkennung, mit der bisher nicht erkannte Fehler identifiziert werden können – ein Bereich, in dem herkömmliche Qualitätskontrollsysteme versagen. Um dies zu erreichen, schlagen wir den Einsatz eines mit einer Kamera ausgestatteten Roboterarms vor, der ein flexibles und anpassungsfähiges Inspektionssystem schafft, das eine Vielzahl von Produkten effizient handhaben kann.
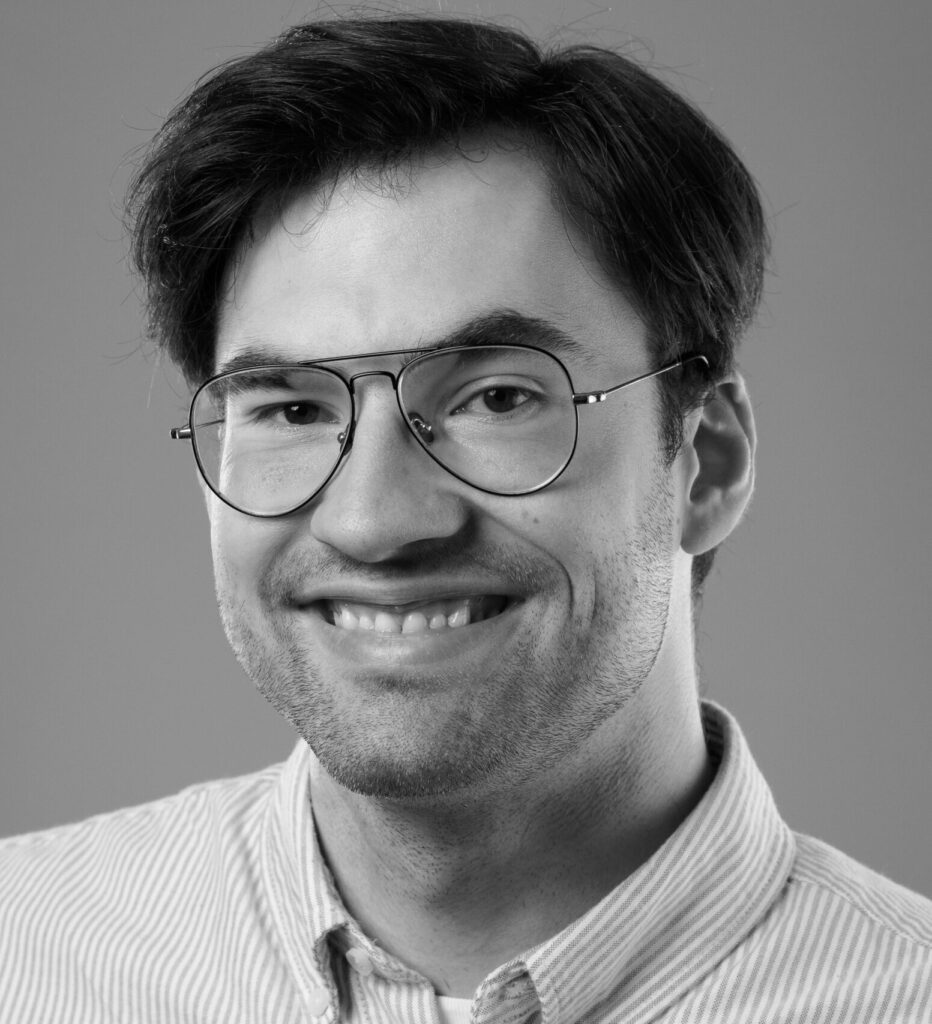
Extending Operational Design Domains of Automated Driving Systems, using Vehicle to Everything
Automatisierte Fahrzeuge befinden sich in der fortlaufenden Entwicklung, und mit den SAE definierten Automatisierungsstufen sind erste Level-3-Fahrzeuge auf öffentlichen Straßen im Einsatz. Bei Level 3 übernimmt das Fahrzeug unter bestimmten Bedingungen die Kontrolle, während der Fahrer weiterhin für die Kontrolle bei Ausnahmen verantwortlich bleibt. Für die Automobilindustrie bedeutet dies, dass die Sicherheit bei jedem Verkehrsgeschehen gewährleistet sein muss. Um diese Sicherheit zu gewährleisten, werden die Bedingungen für die Nutzung einer automatisierten Fahrfunktion als „Operational Design Domain“ (ODD) beschrieben. Ein ODD umfasst verschiedene Faktoren wie Wetter, Verkehr, verfügbare Komponenten und Konnektivität. Ziel des Projekts ist es, zu untersuchen, wie neue Technologien wie Vehicle-to-Everything (V2X) dazu beitragen können, die ODDs zu erweitern und sicherer zu gestalten.
V2X ermöglicht es Fahrzeugen, mit anderen Fahrzeugen und der Infrastruktur zu kommunizieren, wodurch Informationen bereitgestellt werden, die herkömmliche Sensoren nicht liefern können. Dies könnte beispielsweise eine frühzeitige Warnung vor Gefahren auf der Strecke ermöglichen, noch bevor sie von den Fahrzeug-Sensoren erkannt werden. Die Forschung soll einen Vergleich zwischen traditionellen Sensoransätzen und V2X-unterstützten Ansätzen anstellen, um die Erweiterung und Verbesserung der ODDs zu evaluieren und die Sicherheitsaspekte zu gewährleisten. Ein integrativer Ansatz zur Beschreibung und Überwachung von ODDs soll entwickelt werden, um die Auswirkungen der neuen Technologien auf die Sicherheit und die Erweiterung von ODDs zu bewerten.
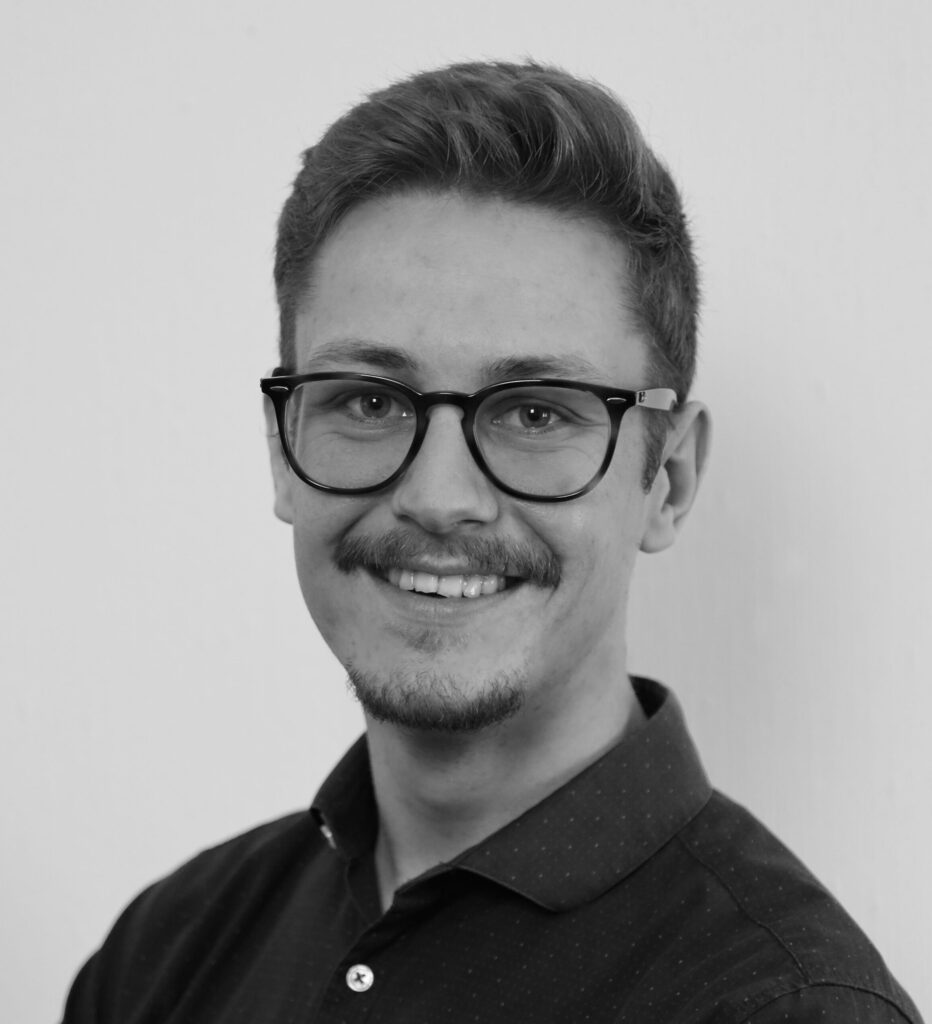
Hybrides simulationsgestütztes Regelungssystem für die adaptive Prozessführung im Laser Powder Bed Fusion Prozess
Die additive Fertigung von Metallbauteilen hat sich in den letzten Jahren als zukunftsweisende Technologie etabliert und ermöglicht die Herstellung hochkomplexer Bauteile mit erheblichen Effizienzvorteilen und Gestaltungsmöglichkeiten.
Das L-PBF-Verfahren ist ein verbreitetes additives Fertigungsverfahren, bei dem Metallpulver durch einen Laser selektiv aufgeschmolzen wird. Die Wahl der Prozessparameter, wie der Laserstrahlleistung, hat dabei einen entscheidenden Einfluss auf die Bauteilqualität, z.B. auf die Oberflächenbeschaffenheit oder die Bauteildichte.
In dieser Arbeit wird die gezielte Anpassung von Prozessparametern untersucht, um die Grenzen der Aufbaubarkeit von Bauteilen weiter zu verschieben. Der Fokus liegt dabei auf der Verwendung adaptiver Prozessparameter, die sowohl die Belichtungsstrategie als auch die Bauteilgeometrie berücksichtigen. Die Prozessparameter werden auf Basis einer Simulation in Kombination mit ausgewählter Messtechnik definiert, die eine Echtzeitbewertung des Fertigungsprozesses ermöglicht. Durch den Einsatz der resultierenden adaptiven Prozessparameter soll eine signifikante Steigerung der Bauteilqualität und Geometriefreiheit erreicht werden. Diese Arbeit wird in Zusammenarbeit mit der Firma Aconity3D GmbH durchgeführt.
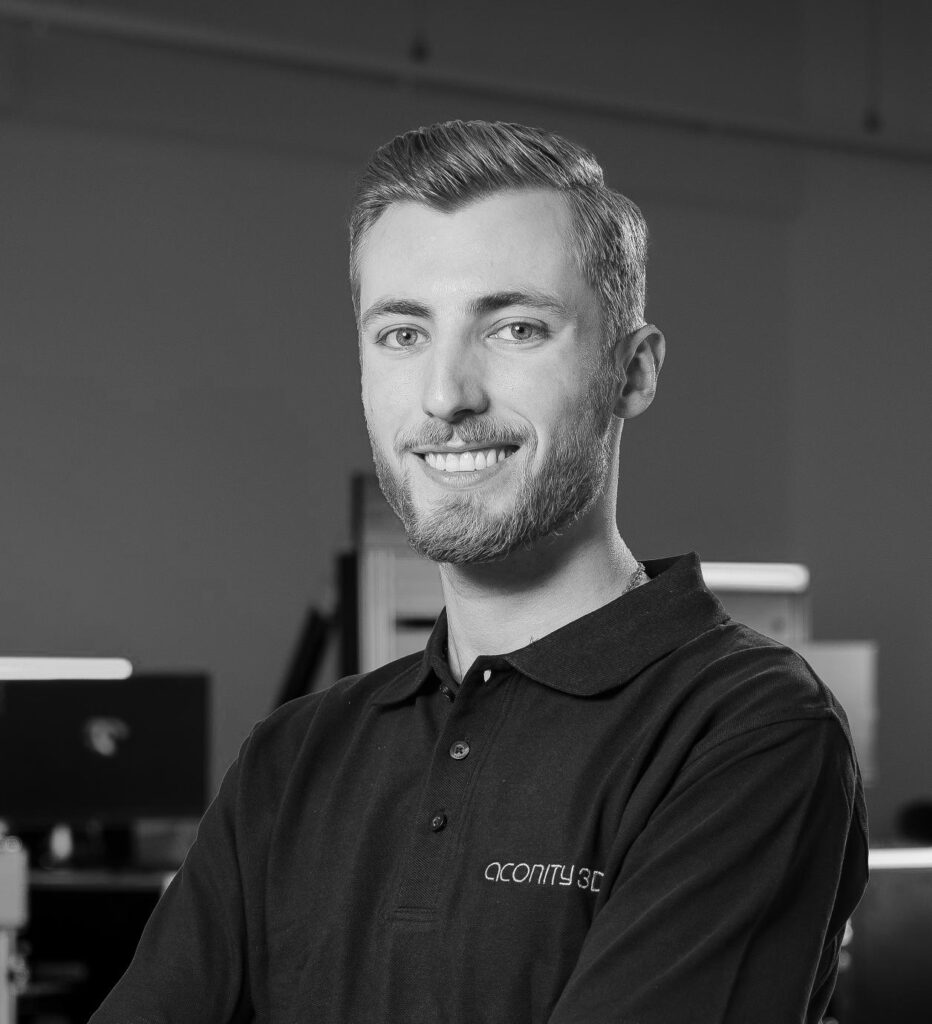
Abgeschlossene Promotionen
Ability based digital support using Gamification for Industry 4.0
Kooperierende Hochschule: RMIT University (Australien)
Im Zuge von Industrie 4.0 müssen Produktionsumgebungen stetig adaptiert werden. Um dies zu bewältigen, bedarf es flexibler und effizienter Arbeitsumgebungen. Zudem müssen sich die Beschäftigten regelmäßig auf neue Arbeitsabläufe und neue Produktionsprozesse einstellen. Ein ständiger und effizienter Lernprozess ist unabdingbar, um eine höhere Flexibilität in der Belegschaft zu erreichen. Darüber hinaus müssen die Mitarbeiter angemessen unterstützt werden, um die steigende Arbeitskomplexität zu bewältigen.
Derzeit werden in der Industrie die Mitarbeitenden on-the-job in neue Varianten, Produkte und Produktionsprozesse eingearbeitet. Während der Arbeit liefern digitale Unterstützungssysteme Informationen, z. B. durch Augmented-Reality-Systeme (AR), während Sensorsysteme die Handlungen kontrollieren. Die bestehenden digitalen Unterstützungssysteme bleiben jedoch unflexibel, indem sie jedem Arbeiter die gleiche Unterstützung bieten, ohne dabei die berufliche Erfahrung und das Wissen zu berücksichtigen. Dieser Ansatz kann zur Ermüdung von Spezialisten und zur Überlastung von Auszubildenden führen. Durch die ständige Nutzung der Unterstützungssysteme können zudem unerwünschten Abhängigkeiten vom System entstehen.
Das hier vorgestellte Forschungsprojekt hat zum Ziel, adaptive und fehlertolerante Unterstützungssysteme zu schaffen, die personalisierte Anweisungen entsprechend den Benutzeraktionen anzuzeigen. Ein Schwerpunkt liegt dabei auf der Integration von Gamification-Strategien in Produktionsumgebungen. Die Spielelemente sollen die Arbeiter motivieren, individuelle Unterstützung ermöglichen und die Flexibilität und Arbeitsleistung erhöhen.
In einem ersten Schritt wurde ein Gamification-Framework für manuelle Arbeit im Fertigungsbereich entwickelt. In einem zweiten Schritt wurde das Gamification Framework für eine Virtual Reality (VR) Trainingsumgebung umgesetzt. Hierfür wurde der bestehende Handarbeitsplatz der Industrie 4.0 Modellfabrik inklusive seiner Funktionalitäten in der virtuellen Welt abgebildet und verschiedene Montageaufgaben integriert. Dem Nutzenden wird es hierdurch ermöglicht, in einer individuellen Geschwindigkeit die einzelnen Level der VR Trainingsumgebung und hierdurch die einzelnen Montagesequenzen zu erlernen.
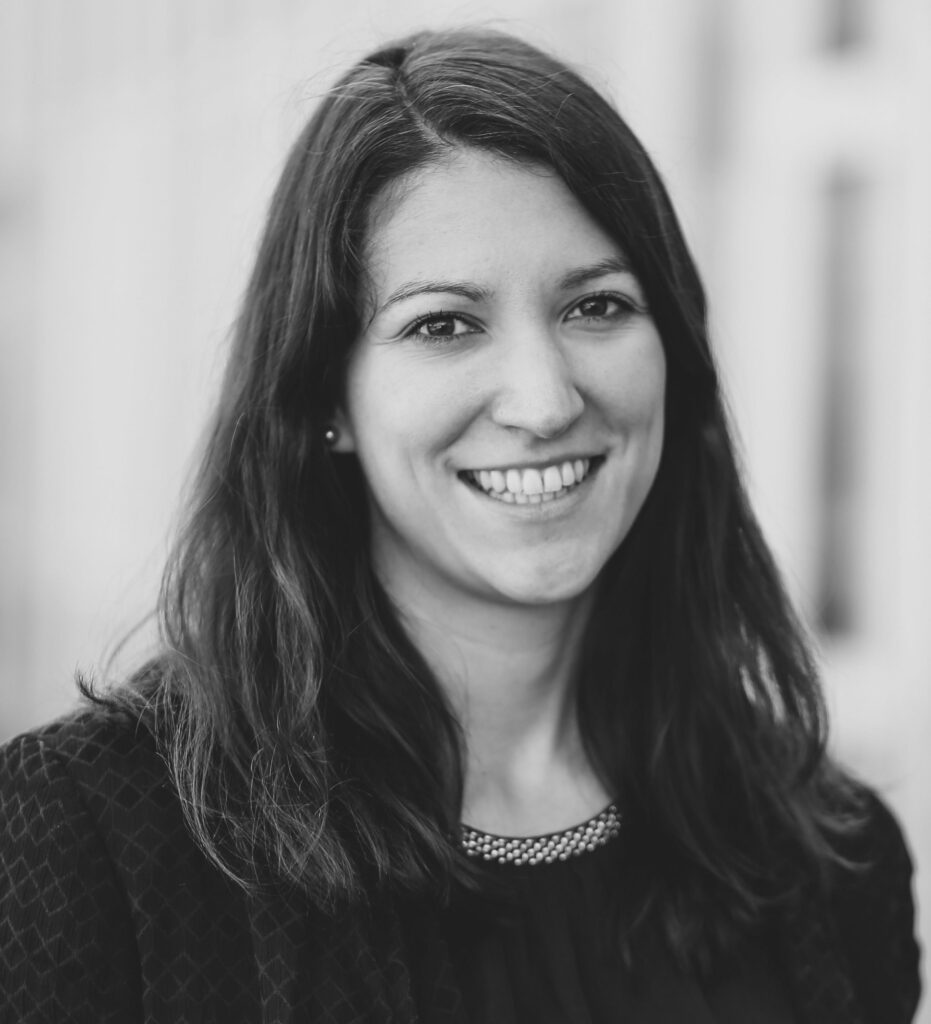
Multi-agent systems to control, simulate and optimize resilient smartfactories
Kooperierende Hochschule: RMIT University (Australien)
Gerade im Mittelstand ist heute ein breites Spektrum unterschiedlicher proprietäre Systemlösungen vorhanden. Diese basieren in der Regel auf monolithischer Software, die den neuen Anforderungen an eine universelle, anwendungsübergreifende Kommunikation nicht gerecht werden. Wie im Rahmen von Industrie 4.0 vorgeschlagen, müssen klassische Strukturen aufgebrochen werden, um dem Wunsch nach integrierbaren, flexiblen und skalierbaren Systemen nachzukommen. Das Referenz Architektur Modell RAMI 4.0 (DIN 91345) bietet den Rahmen und beschreibt sowohl die Datensicht als auch die prinzipielle Kommunikation zwischen Industrie 4.0-Assets und der Infrastruktur.
Diese Arbeit verfolgt den Ansatz ein auf die Problemstellungen der Automatisierungs-technologie zugeschnittenes Framework auf der Basis von Mehragentensystemen bereit zu stellen. Als Agenten sind konfigurierte Anwendungen nach dem Microservice-Gedanken zu verstehen, die unter anderem als zentrale Vermittlungsstelle zwischen Datensätzen und Datenquellen dienen. Jede (aktive) Partei, d.h. Kunde, Auftrag, Maschine oder Produkt, erhält so eine dezentrale Intelligenz, mit der sie sich selbst verwaltet. Dies ermöglicht sowohl ganzheitliche Implementierungen über die gesamte Unternehmensstruktur als auch leicht zu integrierende und flexible spezifische Lösungen mit zu geringem Anpassungsaufwand.
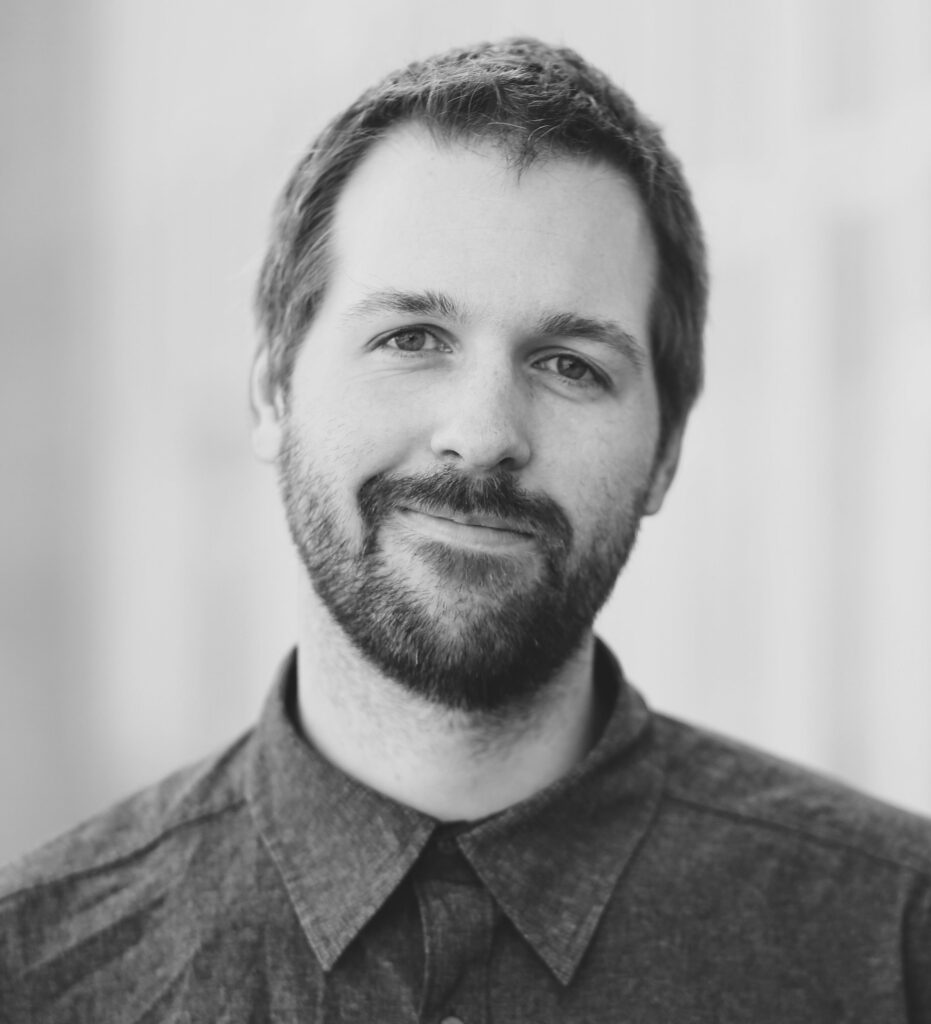
Development of an Autonomous Mobile Manipulator for Human-Robot Collaborative Industrial Environments
Kooperierende Hochschule: Tshwane University of Technology (Südafrika)
Heutige Produktionsstrukturen sind größtenteils für konstant große Produktionschargen und definierte Produkte ausgelegt. Allerdings hat in den letzten Jahren die Nachfrage nach kundenspezifischen bzw. benutzerdefinierten Produkten stark zugenommen und somit die Anforderungen an die industrielle Automatisierung verändert. Die Robotik stellt eine der Kerntechnolgien dar, um die Flexibilität neuer und bereits bestehender Produktionsumgebungen zu erhöhen.
Der Einsatz autonomer mobiler Manipulatoren im Produktionsprozess ist ein Ansatz für die Umsetzung einer flexibleren und agileren Automatisierung. Die Soft- und Hardwarekomponenten eines solchen autonomen industriellen mobilen Manipulators (AIMM) müssen den besonderen Anforderungen einer flexiblen industriellen Produktionsumgebung entsprechen.
Diese Arbeit befasst sich mit der Entwicklung und Implementierung eines autonomen mobilen Manipulators, der mit menschlichen Arbeitern in einem industriellen Produktionsszenario zusammenarbeitet. Hierbei werden alle Kernbereiche der mobilen Manipulation: Mapping, Lokalisierung, Pfadplanung, visuelles Servoing, Arbeitsraumüberwachung sowie Bahnplanung abgedeckt. Trotz der Tatsache, dass in den letzten Jahren viele Forschungsarbeiten das Thema der mobilen Manipulation behandelt haben, ist diese Technologie noch kein Bestandteil heutiger Produktionsprozesse. Der Grund hierfür liegt in der hohen Komplexität des Gesamtsystems.

Design and Control of a climbing Robot for Wind Turbines
Kooperierende Hochschule: Tshwane University of Technology (Südafrika)
Windkraftanlagen (WA) gewinnen an Bedeutung für eine nachhaltige Energieversorgung. Der Zugang für die Wartung der Strukturteile ist aufgrund der schwierigen Wetterbedingungen und der großen Dimensionen moderner Windkraftanlagen problematisch. Der aktuelle Stand der Technik beim Zugang zu den Strukturen von Windkraftanlagen ist der Einsatz von Industriekletterern und seilgestützten Wartungsplattformen. Für beide Lösungen sind aufgrund der begrenzten Stabilität gegenüber Windkräften stabile Wetterbedingungen erforderlich.
Diese Arbeit trägt zur Entwicklung eines Turmkletterroboters (TKR) bei. Die Konstruktion verwendet einen auf Reibung basierenden Klettermechanismus ohne die Notwendigkeit von Seilen. Dadurch kann die Wartung auch bei instabilen Wetterbedingungen durchgeführt werden. Der Klettermechanismus hat zwei Subsysteme für die Fortbewegung und die Adhäsion. Reibungsbasiertes Klettern erfordert Adhäsionskräfte. Der Adhäsionsmechanismus ist auf verschiedene Turmdurchmesser einstellbar. Bei der Entwicklung des TKR wurden mechanisches Design, Sensorintegration und Controller-Layout kombiniert. Das primäre Ziel ist die Optimierung der Roboterkinematik und -dynamik, wobei die Adhäsionskräfte an die Tragfähigkeit des Turms angepasst werden müssen.
Der TKR stellt eine mobile autonome Plattform für verschiedene WA-Wartungsanwendungen dar. Fortschrittliche mobile Robotik auf Basis des Robot Operating System (ROS) ist die Schlüsseltechnologie, die es dem TKR ermöglicht, autonom zu arbeiten.
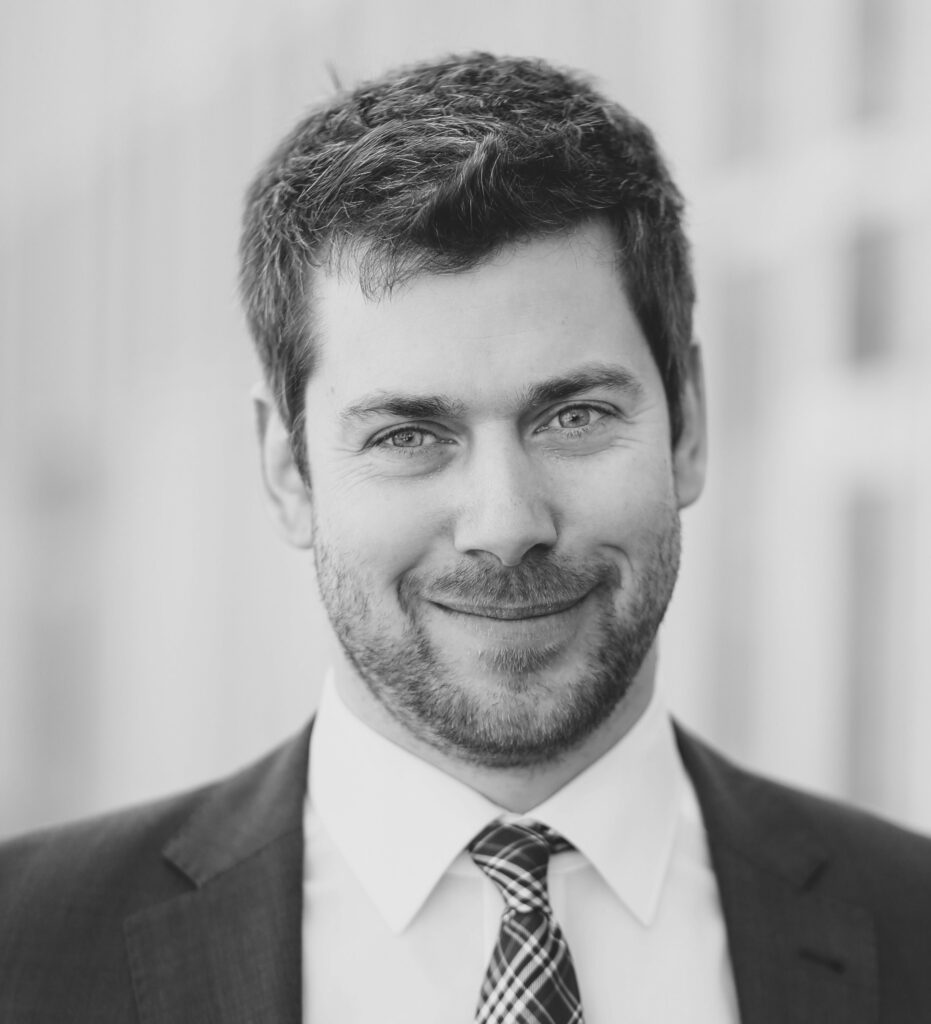
Basic research on direct printed injection molds made from high performance plastics
Kooperierende Hochschule: TUC-Technical University of Cluj-Napoca (Rumänien)
Die fertigende Industrie ist zunehmend auf innovative Technologien angewiesen, um schnell und flexibel Güter zu produzieren. Hier kristallisiert sich die Additive Fertigung als einer der jüngsten und wichtigsten Fertigungsverfahren heraus. Das sogenannte Schichtbauverfahren, auch unter dem Begriff 3D-Druck bekannt, ermöglicht durch die Verfahrensart und diversen Materialien ungeahnte Möglichkeiten der Fertigung. Nahezu jede Geometrie ist mit nur einer Anlage realisierbar. Mit dieser Technologie können Prozessketten entscheidend beeinflusst und verkürzt werden. Dies reduziert die Fertigungszeit, kann den Einsatz von Ressourcen minimieren, reduziert den maschinellen Aufwand und folglich auch die Kosten.
Diese Eigenschaften sind für den Einsatz bei der Werkzeugherstellung überaus vorteilhaft. Die Herstellung eines Spritzgusswerkzeugs ist sehr kosten- sowie zeitintensiv. Bei der Auslegung eines Werkzeuges wird ein fundiertes Knowhow vom Konstrukteur und vom Anlagentechniker benötigt. Doch auch mit viel Erfahrung sind mehrere iterative Schritte notwendig, um zum endgültigen Werkzeug zu gelangen. Die Entwicklungsdauer ist demnach enorm.
An dieser Stelle soll die additive Fertigung ihren Einsatz finden und die Möglichkeit zu einer Effizienten Werkzeugentwicklung eröffnen. Ferner soll hierzu der Einsatz von sogenannten Hochleistungspolymeren verhelfen. Die hohe Temperaturbeständigkeit und die hohen mechanischen Eigenschaften sind dabei das wichtigste Auswahlkriterium für den geplanten Einsatz als Werkzeugmaterial.
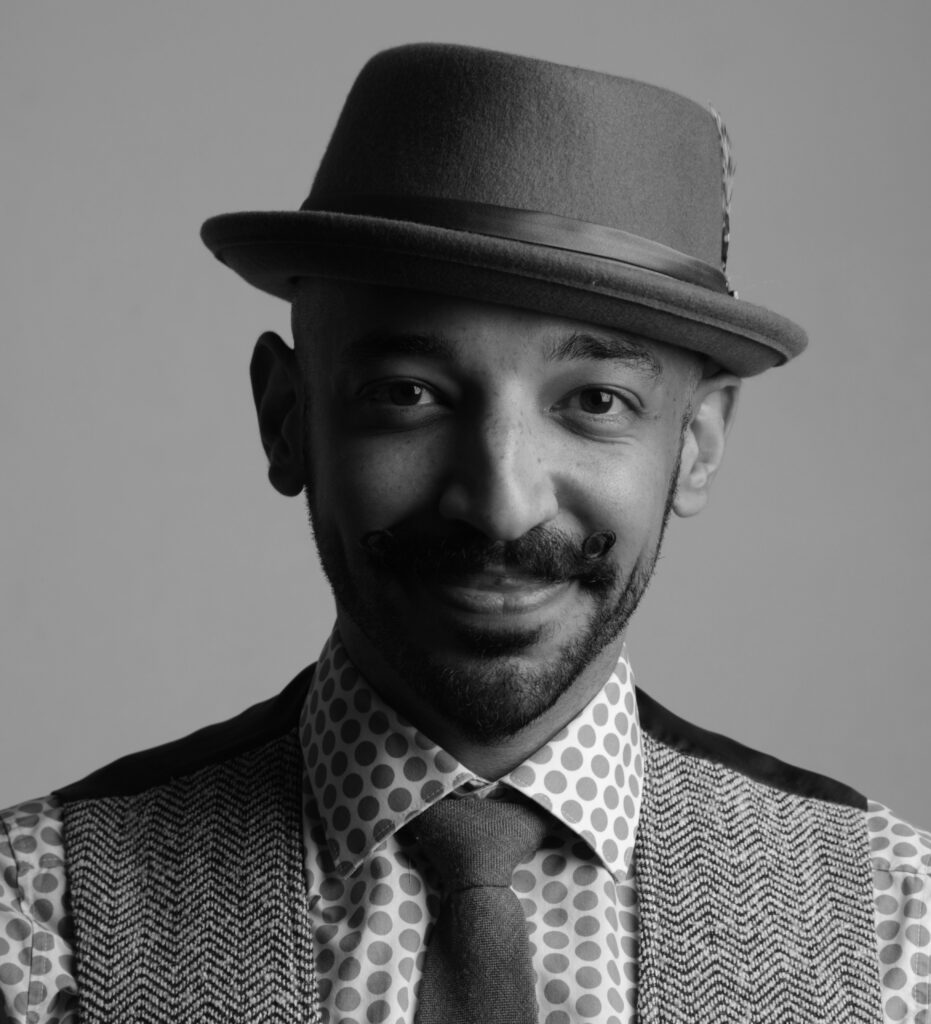
Flexibilization of Production Systems through Additive Manufacturing
Kooperierende Hochschule: TUC-Technical University of Cluj-Napoca (Rumänien)
Die erfolgreiche Etablierung eines wirtschaftlich sinnvollen Flexibilitätsgrades stellt eine große Herausforderung für Unternehmen dar. Die bestehenden Flexibilitätstheorien der letzten Jahrzehnte sind durch die Grenzen der Flexibilisierung von Produktionssystemen mittels konventioneller Fertigungstechnologien zwangsläufig auf wiederkehrende Probleme und Gestaltungsgrenzen gestoßen.
Hier verbirgt sich ein großes Potenzial in einem Überdenken der bestehenden Forschung zur Flexibilisierungstheorie mit Hilfe von additiven Technologien (AM): Aufgrund ihrer natürlich gegebenen sehr hohen Flexibilität bietet AM eine mögliche Lösung, um das Dilemma konventioneller Fertigungstechniken und Flexibilitätskonzepte zu lösen. Um dieses Potenzial zu erschließen, ist jedoch ein neuer Ansatz zur Bewertung der Flexibilität und zum Verständnis der additiven Fertigung erforderlich. Derzeit fehlen jedoch Indikatoren für eine mehrdimensionale Bewertung der AM-Potenziale, eine Integration von AM in die Flexibilitätstheorie sowie eine mehrdimensionale Gesamtbewertung des Nutzens der Technologie abseits der Stückkostenbetrachtung (z.B. Lagerbestände, OEE, Durchlaufzeit, Rüstkosten).
Das Dissertationsprojekt wird ein erster Ansatz sein, um die Forschungslücke zu schließen, indem ein Bewertungsmodell zur Flexibilisierung eines Produktionssystems durch den Einsatz der AM-Technologie untersucht wird. Damit wird ein neuer Ansatz zur Flexibilisierung von Produktionssystemen mittels Additiver Fertigung geschaffen und die bestehenden Flexibilisierungstheorien erweitert.
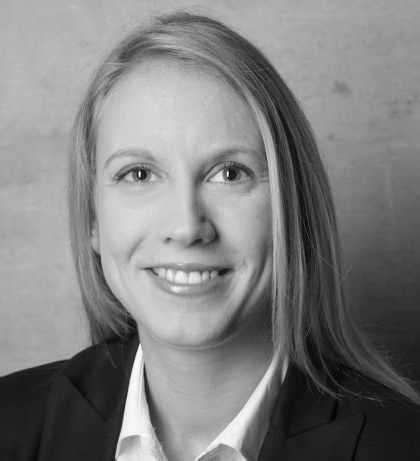